В неустанном стремлении к повышению производительности и эффективности обрабатывающая промышленность переживает всплеск обсуждений, связанных с методами высокоскоростной обработки и передовыми инновациями в области инструментальной обработки. Стремясь к максимальному увеличению производительности при минимизации времени цикла, производители изучают передовые инструментальные материалы, покрытия и геометрию, а также стратегии оптимизации параметров резания и снижения износа инструмента.
Высокоскоростная обработка давно рекламируется как революционное решение в сфере производства, позволяющее сократить производственные циклы и повысить точность. Однако по мере роста требований к эффективности и ужесточению допусков поиск инновационных решений в области обработки усилился. Это привело к возобновлению интереса к исследованию новых возможностей инструментальной технологии.
Одним из основных факторов этой тенденции является разработка современных инструментальных материалов, обладающих повышенной прочностью, термостойкостью и режущей способностью. Такие материалы, как керамика, карбид и кубический нитрид бора (КНБ), приобретают всё большую популярность благодаря своей способности выдерживать высокие нагрузки высокоскоростной обработки, что приводит к увеличению срока службы инструмента и сокращению простоев.
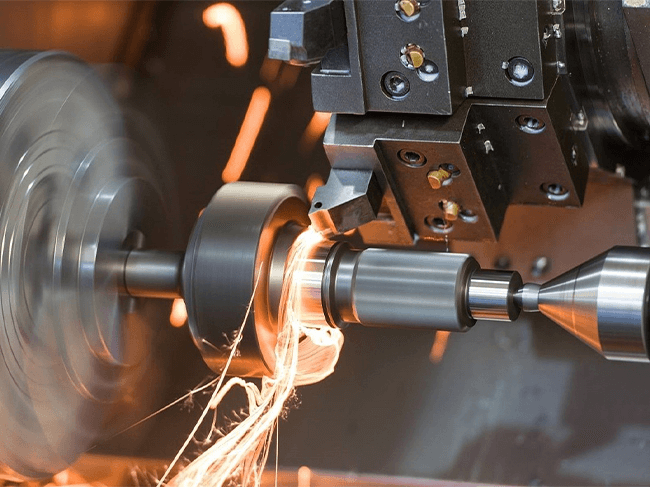
Более того, достижения в области покрытий инструментов произвели революцию в области механической обработки, обеспечив улучшенные смазывающие свойства, износостойкость и термостойкость. Нанопокрытия, покрытия на основе алмазоподобного углерода (DLC) и покрытия из нитрида титана (TiN) — вот лишь некоторые из инновационных решений, которые позволяют повысить скорости резания и подачи, минимизируя трение и налипание стружки.
Помимо материалов и покрытий, геометрия инструмента играет решающую роль в оптимизации производительности обработки. Сложная геометрия, такая как переменный угол наклона спирали, стружколомы и зачистные кромки, улучшает эвакуацию стружки, снижает силы резания и повышает качество поверхности. Используя эти геометрические инновации, производители могут добиться более высокой скорости съёма материала и превосходного качества деталей.
Кроме того, оптимизация параметров резания крайне важна для максимального повышения эффективности высокоскоростной обработки. Такие параметры, как скорость шпинделя, подача и глубина резания, должны быть тщательно откалиброваны для обеспечения баланса между силами резания, стойкостью инструмента и качеством поверхности. Благодаря передовым методам моделирования процесса обработки и системам мониторинга в реальном времени производители могут точно настраивать эти параметры для достижения оптимальной производительности, минимизируя износ инструмента и отходы материала.
Несмотря на значительный прогресс в области высокоскоростной обработки и инноваций в области инструмента, сохраняются проблемы, включая необходимость в обучении квалифицированных рабочих, инвестициях в современное оборудование и интеграции цифровых технологий для оптимизации процессов. Однако потенциальные преимущества весьма существенны, включая повышение производительности, сокращение сроков выполнения заказов и повышение конкурентоспособности на мировом рынке.
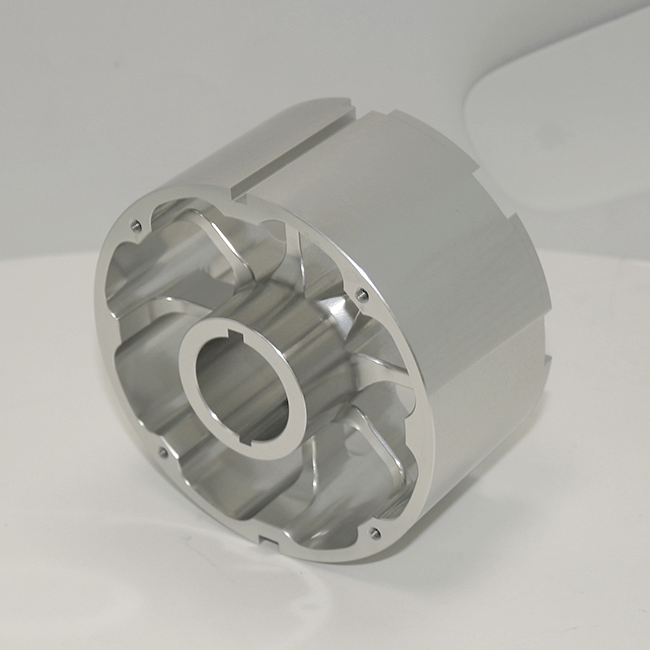
По мере развития производства в цифровую эпоху внедрение высокоскоростных методов обработки и передовых инновационных инструментов готово изменить ландшафт отрасли. Внедряя инновации и инвестируя в передовые решения в области обработки, производители могут оставаться на шаг впереди и выходить на новый уровень эффективности и производительности.
В заключение отметим, что сочетание высокоскоростной обработки и передовых инноваций в области инструментальной обработки представляет собой смену парадигмы в обрабатывающей промышленности, открывая эру беспрецедентной производительности и точности. Благодаря технологиям, движущим вперёд, возможности для инноваций и развития безграничны, что ведёт отрасль к новым вершинам успеха и процветания.
Время публикации: 14 июня 2024 г.